在现代铁路运输的宏大版图中,钢轨作为关键基础设施,其质量与性能直接关乎铁路系统的安全、高效运行。作为专业的冶金项目交钥匙工程供应商,我们深入了解钢轨生产的每一个细节,致力于为客户提供从工艺规划到设备安装调试的一站式解决方案。本文将详细介绍钢轨生产工艺以及我们所配备的先进设备,展现我们在钢轨生产领域的专业实力。
一、钢轨生产工艺全解析
(一)原料准备:品质的基石
1. 精选原料:生产钢轨的主要原料为优质钢铁,通常会选用含有特定合金元素的钢材,如锰(Mn)、铬(Cr)、钒(V)等。这些合金元素在提升钢轨性能方面发挥着关键作用。锰元素能够显著提高钢材的硬度与韧性,增强其抵抗磨损和变形的能力;铬元素可提升钢轨的抗腐蚀性;钒元素则有助于细化晶粒,改善钢材的综合力学性能。
2. 精准配比:在原料配比过程中,精确性至关重要。针对不同型号的钢轨,我们严格遵循精确到小数点后两位的钢铁与合金元素比例进行混合。例如,对于某一特定高速铁路用钢轨,其合金元素的配比经过大量实验和模拟分析确定,以确保每一批次原料都具备高度的一致性,为后续生产出质量稳定的钢轨奠定坚实基础。
3. 熔炼与精炼:采用先进的电炉或转炉熔炼技术,将原料加热至高温,使其完全熔化为钢水。在熔炼过程中,通过添加精炼剂等手段,去除钢水中的杂质,如硫(S)、磷(P)等。这些杂质的存在会降低钢轨的性能,如硫会使钢材产生热脆性,磷则会导致冷脆性。利用直读光谱仪等先进检测设备,实时监测钢水的成分,确保其纯净度符合严格的标准。经过熔炼和精炼后的钢水,纯净度极高,为后续生产高质量的钢轨提供了有力保障。
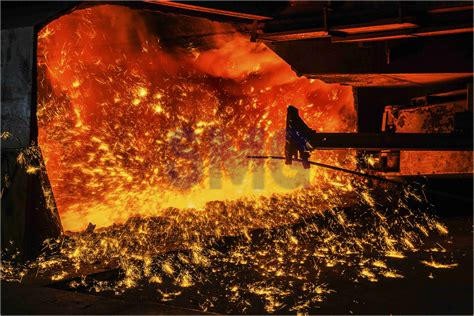
(二)铸造成型:塑造钢轨雏形
1. 模具定制与钢水注入:当钢水达到规定的成分和温度后,便进入铸造成型阶段。此时,钢水会被精准地注入根据钢轨规格和尺寸定制的特定形状模具中。模具的设计经过精密计算和模拟,确保能够精确地塑造出钢轨的初始形状。在注入钢水时,严格控制注入速度和压力,以保证钢水能够均匀地填充模具的各个部位,避免出现气孔、缩孔等缺陷。
2. 加热与冷却处理:注入模具的钢水随后进入加热和冷却工序。首先,通过加热使钢水在模具内充分流动,填补可能存在的微小空隙,进一步提高钢轨的致密度。接着,采用特定的冷却工艺,如控制冷却速度和冷却方式,使钢水逐渐凝固成固态的钢轨坯。在这个过程中,高温和高压的作用至关重要。高温能够使钢水的流动性更好,确保填充的完整性;高压则有助于消除内部的微小缺陷,使钢轨的结构更加紧密,提高其力学性能。例如,在一些先进的铸造工艺中,会对模具施加一定的压力,使钢轨坯在凝固过程中更加致密,从而提升其强度和韧性。经过铸造成型后的钢轨坯,已经具备了钢轨的基本形状,但还需要进一步的加工和处理才能成为合格的钢轨。
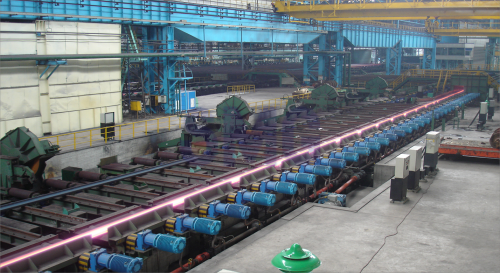
(三)轧制工艺:赋予钢轨精准尺寸与性能
1. 多道轧制与先进技术应用:铸造成型的钢坯被送入轧机,开启关键的轧制工艺。在轧制过程中,钢坯要经历多次轧制,每次轧制都使其逐渐发生塑性变形,最终形成符合标准尺寸和形状的钢轨。我们采用先进的四辊或万能轧制技术。四辊轧机通过上下轧辊和左右立辊的协同作用,可以对钢轨的轨头、轨腰和轨底进行均匀的轧制,确保其尺寸精度和表面质量。万能轧制技术则更加灵活,能够适应不同规格和形状的钢轨轧制需求,通过调整轧辊的位置和角度,实现对钢轨断面的全方位加工。
2. 热处理与轧制协同:在轧制过程中,热处理工艺与轧制紧密配合。适时的加热和冷却处理,能够有效改善钢轨的组织结构,提高其强度、韧性和耐磨性。例如,在轧制前对钢坯进行加热,使其达到合适的轧制温度,能够降低轧制力,提高轧制效率;在轧制后进行淬火和回火处理,可以使钢轨获得良好的综合力学性能。通过精确控制轧制和热处理的参数,如轧制温度、道次、变形量、加热时间和冷却速度等,我们确保每一根钢轨都具备卓越的结构密度和机械性能,能够满足各种严苛的使用环境和工况要求。
(四)表面处理:提升钢轨使用寿命与外观质量
1. 除锈工艺:经过轧制后的钢轨,虽然已经具备基本性能,但为进一步提高其使用寿命和外观质量,还需进行表面处理。首先进行的是除锈工艺,我们采用先进的抛丸除锈或酸洗除锈方法。抛丸除锈通过高速旋转的叶轮将钢丸抛射到钢轨表面,利用钢丸的冲击力去除表面杂质,这种方法效率高、效果好,且对环境友好。酸洗除锈则是利用酸液与铁锈发生化学反应,将其溶解去除。在除锈过程中,严格控制工艺参数,确保除锈效果的同时,避免对钢轨基体造成损伤。
2. 喷砂与喷漆:除锈后的钢轨进行喷砂处理,通过高压空气将石英砂等磨料喷射到钢轨表面,使表面形成均匀的粗糙度,增加后续喷漆的附着力。喷砂处理后的钢轨表面呈现出均匀的银灰色,质感细腻。随后进行喷漆工艺,选用高质量的防腐漆,采用自动化的喷漆设备进行喷涂,确保漆层均匀、厚度一致。喷漆不仅能够提高钢轨的抗腐蚀性,还能起到一定的装饰作用,使钢轨表面更加美观。
3. 质量检测与追溯:在表面处理完成后,对每一根钢轨进行严格的质量检测,包括外观检查、尺寸测量和性能测试等。利用先进的无损检测设备,如超声波探伤仪、磁粉探伤仪等,对钢轨内部和表面进行全面检测,确保无任何缺陷。对合格的钢轨进行清晰标记,标注产品型号、规格、生产日期、生产批次等信息,以便于追溯和管理。
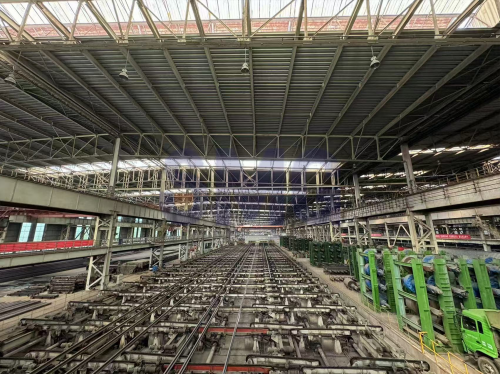
(五)调质处理:优化钢轨性能的关键环节
1. 调质原理与工艺:调质处理是钢轨生产过程中的关键环节,它基于金属材料的热处理原理,通过对钢轨进行特定的加热和冷却处理,调整其组织结构和性能,使其具备更好的强度和韧性。首先将钢轨加热到适当的温度,使其内部组织奥氏体化,然后迅速冷却,获得马氏体或贝氏体等高强度的组织。最后进行高温回火,使马氏体或贝氏体组织转变为回火索氏体,这种组织具有良好的综合力学性能,强度、韧性和塑性得到了很好的平衡。
2. 精确参数控制:在调质处理过程中,精确控制加热温度、保温时间、冷却速度和回火温度等参数至关重要。例如,加热温度过高或保温时间过长,会导致晶粒粗大,降低钢轨的性能;冷却速度过快,则可能产生裂纹等缺陷。我们采用先进的自动化控制系统,实时监测和调整这些参数,确保调质处理的效果稳定可靠。经过调质处理后的钢轨,能够承受列车运行时产生的巨大压力和冲击力,同时具备良好的抗疲劳性能,大大延长了钢轨的使用寿命。在实际应用中,经过调质处理的钢轨在高速铁路、重载铁路等领域表现出色,为铁路运输的安全和高效提供了有力保障。
二、先进设备助力钢轨生产
(一)熔炼设备
1. 高效电炉:我们配备的先进电炉采用了最新的节能技术,能够快速将原料加热至所需温度,并且在熔炼过程中能够精确控制温度和化学成分。其大容量的设计可以满足大规模生产的需求,同时具备高效的除杂能力,确保钢水的纯净度。
2. 智能转炉:智能转炉配备了自动化的控制系统,能够根据钢水的成分和温度实时调整吹氧、造渣等操作参数。其先进的炉衬材料具有高耐火性和抗侵蚀性,延长了设备的使用寿命,提高了生产效率。
(二)铸造设备
1. 高精度模具制造设备:为了确保模具的精度和质量,我们拥有先进的模具制造设备,如数控加工中心、电火花加工机床等。这些设备能够制造出复杂形状的模具,满足不同规格钢轨的生产需求。模具的表面经过特殊处理,具有良好的耐磨性和脱模性能,保证了铸造成型过程的顺利进行。
2. 先进的钢水浇注系统:我们的钢水浇注系统采用了先进的计量和控制技术,能够精确控制钢水的注入速度和压力。配备的自动浇注设备可以实现无人操作,提高了生产的稳定性和一致性,减少了人为因素对产品质量的影响。
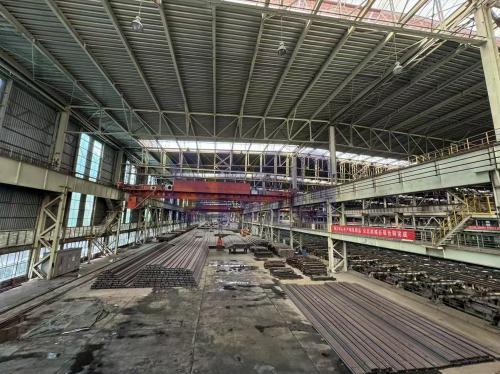
(三)轧制设备
1. 高性能四辊轧机:四辊轧机是我们轧制工艺的核心设备之一,其采用了高精度的轧辊和先进的传动系统,能够实现对钢轨的高精度轧制。轧辊的材质经过特殊处理,具有高硬度和耐磨性,保证了长时间的稳定运行。同时,轧机配备了自动化的板形控制系统,能够实时监测和调整钢轨的板形,确保产品的尺寸精度和表面质量。
2. 万能轧机:万能轧机具有高度的灵活性,能够适应不同规格和形状的钢轨轧制需求。其轧辊的位置和角度可以通过计算机控制系统进行精确调整,实现对钢轨断面的全方位加工。该设备还配备了先进的在线检测系统,能够实时监测轧制过程中的各项参数,及时发现和解决问题,保证产品质量。
(四)表面处理设备
1. 自动化抛丸除锈设备:自动化抛丸除锈设备采用了高效的抛丸器和先进的输送系统,能够快速、均匀地去除钢轨表面的铁锈和杂质。设备的抛丸量和抛射角度可以根据钢轨的材质和表面状况进行调整,确保除锈效果达到最佳。同时,配备的粉尘收集系统能够有效减少环境污染,符合环保要求。
2. 高精度喷漆设备:我们的高精度喷漆设备采用了先进的喷涂技术,能够实现对钢轨表面的均匀喷漆。设备配备了自动化的喷枪和喷漆机器人,可以根据钢轨的形状和尺寸进行精确喷涂,保证漆层的厚度和质量。同时,喷漆车间采用了环保型的通风和废气处理系统,确保生产过程中的环保要求。
(五)检测与控制设备
1. 先进的无损检测设备:为了确保钢轨的质量,我们配备了先进的无损检测设备,如超声波探伤仪、磁粉探伤仪、涡流探伤仪等。这些设备能够对钢轨内部和表面的缺陷进行快速、准确的检测,检测精度达到行业领先水平。同时,设备还具备数据存储和分析功能,能够对检测结果进行统计和分析,为生产过程的优化提供依据。
2. 自动化控制系统:整个钢轨生产过程采用了先进的自动化控制系统,实现了对生产设备的集中监控和管理。控制系统通过传感器实时采集生产过程中的各项参数,如温度、压力、速度等,并根据预设的程序进行自动调整和控制。操作人员可以通过计算机界面实时监控生产过程,及时发现和解决问题,提高了生产的稳定性和效率。
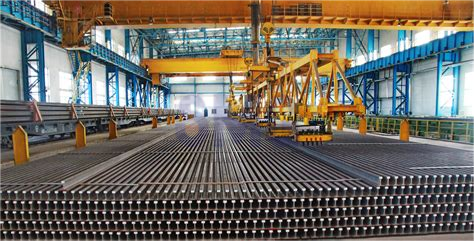
作为专业的冶金项目交钥匙工程供应商,我们为客户提供高品质的钢轨生产解决方案。从原料准备到成品出厂,每一个环节都经过严格的质量控制,确保生产出的钢轨能够满足各种严苛的使用要求。